Industrial News
What are the differences between aluminum tube production for cosmetic packaging vs pharmaceutical packaging?
Views : 34907
Author : 李スコット
Update time : 2020-09-08 12:57:58
I often encounter customers in the cosmetics industry, asking about aluminum tube packaging for cosmetics, commonly filled with hair dye, hand cream, body lotion, mascara, etc. different from those used for medicinal purposes. As a medicinal aluminum tube manufacturer, it isn't easy to produce suitable aluminum tubes for cosmetics.
However, if cosmetics customers are willing to adapt to a higher-cost, higher-level clean room environment, the higher-capacity factories can build dual aluminum tube production lines to produce medicinal and cosmetic tubing. There are only a few factories in China using this concept on this scale. So let's address the similarities and the differences in the aluminum hoses used in these two similar industries for further education and information.
The materials, coatings, and packaging materials used in cosmetic aluminum tubes and pharmaceutical aluminum tubes are the same. All of them are created by stamping out 99.95%+ pure aluminum wafers. They all use polyurethane inks, epoxy resin inner coating materials, and rubber tail coatings. The plastic bags, packaging boxes, and boxes used are also of the same specifications and materials.
2. Production Process:
The production process is precisely the same: mixing, stamping, threading, internal spraying, primer coating, printing, capping, tail coating, and boxing.
3. Appearance specifications:
The appearance specifications and dimensions produced by the production process have identical standards, such as diameter, thickness, thread pitch, softness, hardness, etc. Those are all the same for aluminum tube ointment packaging. The molds, fixtures, or printing tools used with these specifications typically utilize either metric standards, EU standards, or a mixture of both.
4. Inspections standards and other specifications:
Both the in-line inspection process and the finished product inspection of aluminum tubes follow the same methods. These include softness and hardness testing, length and thickness measurements, weight testing, ink color fastness testing, conductivity testing of primer, etc. - all of these are identical.
5. Applicable laws and regulations:
The application of general guidelines is the same, such as national or EU standards, the establishment of fire-fighting facilities, emergency evacuation treatment plans, environmental assessment, environmental protection equipment installation, waste disposal, etc. Regulations and compliance standards remain the same for both types of aluminum container usage.
1. Qualifications for production as mandated by governmental authorities:
In the industrial category of pharmaceutical packaging materials/raw and auxiliary packages - the registration number of the government agency's drug regulatory bureau must be officially recorded. The DMF system is utilized in the production process and inspection standards of the manufacturing facility. Production specifications, supplier information, and personal files must be current. Management must be willing to accept unannounced inspections by government officials. In stark contrast, the cosmetics industry does not have these stringent requirements.
2. Applicability of quality management practices:
The applicable manufacturing management practices are different. Pharmaceutical aluminum tubes follow GMP management guidelines and ISO15378 quality management practices are followed. Generally speaking, the quality management system for cosmetics follows ISO9001 management standards.
3. Control of the production environment:
The high standards for the manufacture of pharmaceutical aluminum hoses of at least one-hundred-thousand units require an IS8 cleanroom facility. The strict control of the positive and negative pressure, temperature and humidity in the workshop, illumination, dust count, colony count, etc., are all set up and managed with the same specifications as the production of different ointment drugs.
Conversely though, the manufacture of packaging aluminum tubes for cosmetics does not need such strict controls. Notwithstanding, however, if aluminum cosmetic tubes are mass-produced in a cleanroom, with stringent quality and cleanliness control, the resulting product will be ideal.
4. Testing of aluminum packaging tubes and materials:
When determining suitable aluminum tube ointment packaging materials for different ointments and liquid pastes, the packaging materials' safety and compatibility, and the type of paste filling is an important consideration, and thus requires corresponding tests to be carefully applied. Test research on the packaging materials must be conducted beforehand to avoid qualitative changes or accidents in the process of production, storage, transportation, use, and preservation, which might result in either minor or severe injuries to personnel and or patients.
The evaluation and testing of cosmetic pastes are equally necessary, as cosmetics products are more weakly acidic or weakly alkaline, and prone to chemical reactions when coming in contact with the surface of pure aluminum tubes, resulting in a shorter shelf life or deterioration of the paste. Therefore, the requirements for the inner coating of the packaging aluminum squeeze tube are higher and stricter. Usually, ammonia water's destructive test is utilized to verify whether the surface coating is adequate, is applied evenly, and can withstand long-term exposure to weak acids and weak bases?
5. Bacteria or microbial indicators:
There is no need to control microbial indicators for external-use ointments. A higher-level process, though, is required for high-risk creams and lotions, and not just for drugs and pharmaceutical outer packaging aluminum tubes. Bacterial or microbial indicators are then necessarily applied by growing bacterial cultures to verify the packaging containers meet sterility standards. This is done by conducting a sterilization process after the packaging is completed.
The sterilization treatment method uses ethylene-oxide on high-risk type packaging products. The material undergoes a specific control process to avoid the pollution of the ointment therein reducing the risk of bacteria or microorganisms invading the body when coming in contact with a wound. Cosmetic tubes, though, generally do not have such concerns or requirements.
Summary
These are the general similarities and differences between the production of ointment packaging aluminum tubes and cosmetic packaging aluminum tubes for customers interested in enhancing their understanding of the subject. I also hope that people within our industry will take the opportunity to explore these aspects further and refine their own general perceptions.
However, if cosmetics customers are willing to adapt to a higher-cost, higher-level clean room environment, the higher-capacity factories can build dual aluminum tube production lines to produce medicinal and cosmetic tubing. There are only a few factories in China using this concept on this scale. So let's address the similarities and the differences in the aluminum hoses used in these two similar industries for further education and information.
First, what are the similarities?
1. Materials:The materials, coatings, and packaging materials used in cosmetic aluminum tubes and pharmaceutical aluminum tubes are the same. All of them are created by stamping out 99.95%+ pure aluminum wafers. They all use polyurethane inks, epoxy resin inner coating materials, and rubber tail coatings. The plastic bags, packaging boxes, and boxes used are also of the same specifications and materials.
2. Production Process:
The production process is precisely the same: mixing, stamping, threading, internal spraying, primer coating, printing, capping, tail coating, and boxing.
3. Appearance specifications:
The appearance specifications and dimensions produced by the production process have identical standards, such as diameter, thickness, thread pitch, softness, hardness, etc. Those are all the same for aluminum tube ointment packaging. The molds, fixtures, or printing tools used with these specifications typically utilize either metric standards, EU standards, or a mixture of both.
4. Inspections standards and other specifications:
Both the in-line inspection process and the finished product inspection of aluminum tubes follow the same methods. These include softness and hardness testing, length and thickness measurements, weight testing, ink color fastness testing, conductivity testing of primer, etc. - all of these are identical.
5. Applicable laws and regulations:
The application of general guidelines is the same, such as national or EU standards, the establishment of fire-fighting facilities, emergency evacuation treatment plans, environmental assessment, environmental protection equipment installation, waste disposal, etc. Regulations and compliance standards remain the same for both types of aluminum container usage.
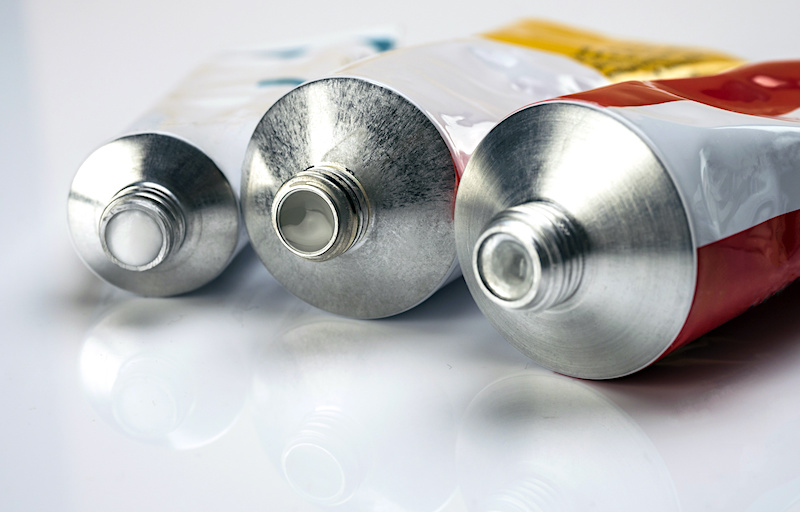
Secondly, what are the differences between the manufacture of aluminum tubes for pharmaceuticals and those for cosmetics?
1. Qualifications for production as mandated by governmental authorities:
In the industrial category of pharmaceutical packaging materials/raw and auxiliary packages - the registration number of the government agency's drug regulatory bureau must be officially recorded. The DMF system is utilized in the production process and inspection standards of the manufacturing facility. Production specifications, supplier information, and personal files must be current. Management must be willing to accept unannounced inspections by government officials. In stark contrast, the cosmetics industry does not have these stringent requirements.
2. Applicability of quality management practices:
The applicable manufacturing management practices are different. Pharmaceutical aluminum tubes follow GMP management guidelines and ISO15378 quality management practices are followed. Generally speaking, the quality management system for cosmetics follows ISO9001 management standards.
3. Control of the production environment:
The high standards for the manufacture of pharmaceutical aluminum hoses of at least one-hundred-thousand units require an IS8 cleanroom facility. The strict control of the positive and negative pressure, temperature and humidity in the workshop, illumination, dust count, colony count, etc., are all set up and managed with the same specifications as the production of different ointment drugs.
Conversely though, the manufacture of packaging aluminum tubes for cosmetics does not need such strict controls. Notwithstanding, however, if aluminum cosmetic tubes are mass-produced in a cleanroom, with stringent quality and cleanliness control, the resulting product will be ideal.
4. Testing of aluminum packaging tubes and materials:
When determining suitable aluminum tube ointment packaging materials for different ointments and liquid pastes, the packaging materials' safety and compatibility, and the type of paste filling is an important consideration, and thus requires corresponding tests to be carefully applied. Test research on the packaging materials must be conducted beforehand to avoid qualitative changes or accidents in the process of production, storage, transportation, use, and preservation, which might result in either minor or severe injuries to personnel and or patients.
The evaluation and testing of cosmetic pastes are equally necessary, as cosmetics products are more weakly acidic or weakly alkaline, and prone to chemical reactions when coming in contact with the surface of pure aluminum tubes, resulting in a shorter shelf life or deterioration of the paste. Therefore, the requirements for the inner coating of the packaging aluminum squeeze tube are higher and stricter. Usually, ammonia water's destructive test is utilized to verify whether the surface coating is adequate, is applied evenly, and can withstand long-term exposure to weak acids and weak bases?
5. Bacteria or microbial indicators:
There is no need to control microbial indicators for external-use ointments. A higher-level process, though, is required for high-risk creams and lotions, and not just for drugs and pharmaceutical outer packaging aluminum tubes. Bacterial or microbial indicators are then necessarily applied by growing bacterial cultures to verify the packaging containers meet sterility standards. This is done by conducting a sterilization process after the packaging is completed.
The sterilization treatment method uses ethylene-oxide on high-risk type packaging products. The material undergoes a specific control process to avoid the pollution of the ointment therein reducing the risk of bacteria or microorganisms invading the body when coming in contact with a wound. Cosmetic tubes, though, generally do not have such concerns or requirements.
Summary
These are the general similarities and differences between the production of ointment packaging aluminum tubes and cosmetic packaging aluminum tubes for customers interested in enhancing their understanding of the subject. I also hope that people within our industry will take the opportunity to explore these aspects further and refine their own general perceptions.
Related News

Why Aluminium Hand Cream Tubes Are the Best Choice
Feb .25.2025
When it comes to packaging hand creams, product developers have several options—plastic tubes, glass jars, pump bottles, and aluminium collapsible tubes. Among these, aluminium hand cream tubes stand out as a superior choice due to their excellent protect

The Hygienic Advantages of Aluminum Pharma Tubes
Nov .25.2024
In the world of pharmaceutical and cosmetic packaging, maintaining hygiene and product safety is paramount. Consumers rely on packaging to protect the integrity of their medications, skincare products, and other personal care items. Pharmaceutical aluminu

7 Benefits of Using Aluminum Pharmaceutical Tubes for Cosmetics
Nov .21.2024
In the competitive world of cosmetics, packaging plays a crucial role in ensuring product safety, efficacy, and consumer appeal. Aluminum pharmaceutical tubes have become a popular choice for cosmetic packaging due to their numerous benefits. Here are sev

Why Aluminum Ointment Tubes are Preferred for Pharmaceutical Packaging
Jul .18.2024
In the pharmaceutical industry, the packaging of products is just as critical as the formulation itself. Aluminum ointment tubes have emerged as the preferred choice for packaging a variety of pharmaceutical products, including ointments, creams, and gels